Rotary compressors are indispensable to air conditioning and refrigeration systems, as they play a crucial role in the refrigeration cycle. They are among the most widely used compressors in the industry, with a variety of designs and configurations to meet different performance requirements. The manufacturing process of rotary compressors is a complex and highly automated procedure that involves multiple steps, from component fabrication to assembly and testing. It is essential to ensure their quality, efficiency, and reliability.
In this blog post, we will take a closer look at the rotary compressor manufacturing process.
Let’s dive right in.
1. Sheet metal processing
The first step in manufacturing the miniature rotary compressor is to mold out the metal sheets into the desired shape and size. The sheets are usually made of steel and are cut into the shape of the compressor housing and other components. The cut sheets are then formed and bent into the desired shape using a press brake.
This process involves applying pressure to the sheet metal to create the necessary bends and curves for the miniature refrigeration compressor housing, motor mount, and other components. Then the different parts of the variable speed direct current inverter compressor are welded together using welding machine.

Main processing workmanship: stamping, welding, cutting, cleaning, heat treatment.
Processing parts: main shell parts, upper shell, lower shell, frame, stator and rotor parts.
The parts processed in the sheet metal workshop are cleaned, spot-checked and sent to the assembly workshop.
Key process: welding, heat treatment
2. Parts processing (mechanical processing)
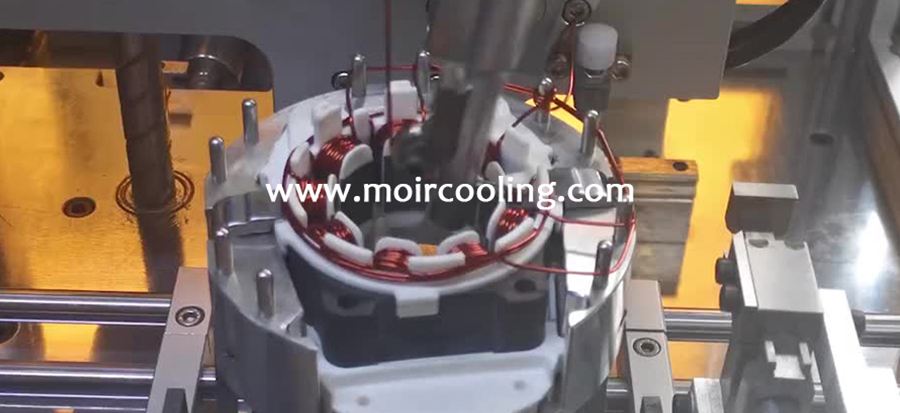
Parts processing workshop is mainly responsible for the processing of the pump of the rotary dc compressor, the pump is called the heart of the compressor.
So the workshop is an important processing workshop. It is set up with the most equipment and the largest investment.
Main machining processes: turning, grinding, cleaning.
Machining components: cylinder, crankshaft, rolling piston, slide, main and sub-bearing
Processing characteristics: The surface processing and dimensional accuracy of parts are controlled in Class II.
Cleaning and inspection requirements require strict process.
Key process: cylinder, crankshaft, rolling piston fine grinding
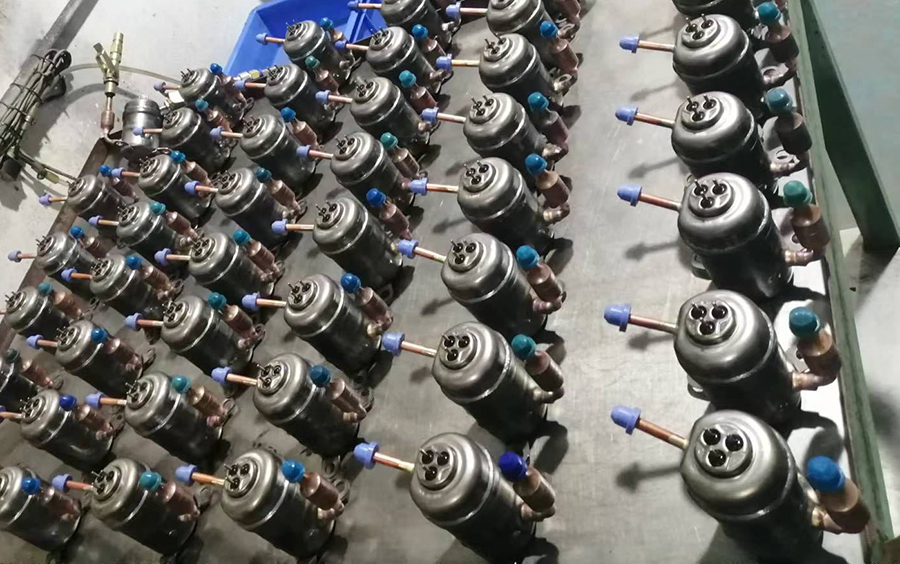
3. Coiled wire (motor) workshop
The winding workshop inserts, shapes and inspects motor stator insulating paper, electromagnetic wires and lead wires.
The process proceeds with a high degree of production automation.
Key process: coil insulation inspection
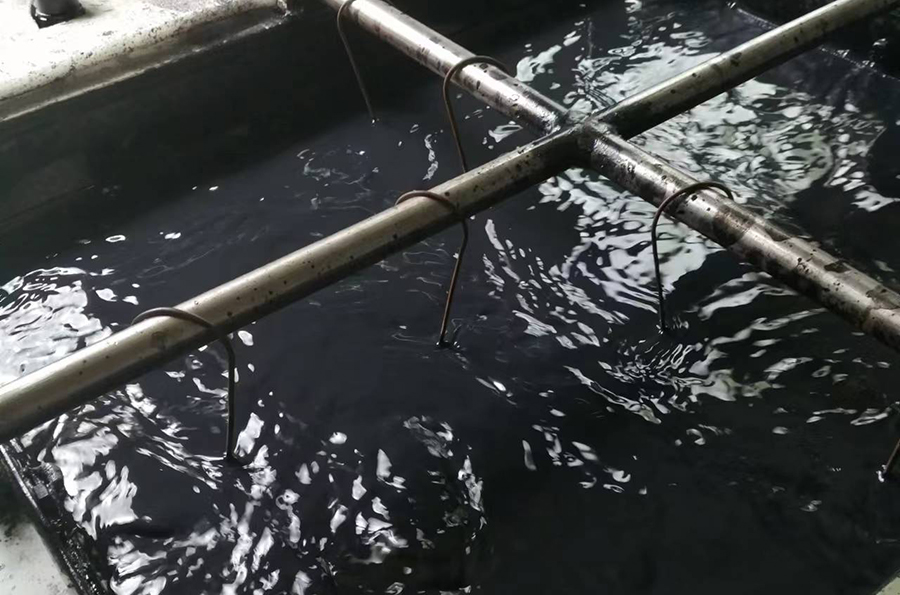
4. Assembly workshop
The assembly workshop is to carry out the matching, assembling, shell welding, surface painting and performance testing of components processed from machining, sheet metal and motor processing.
The inspection items involved are inter-process assembly dimensional inspection, electrical performance inspection, the sealing of the whole machine and the final safety and performance inspection.
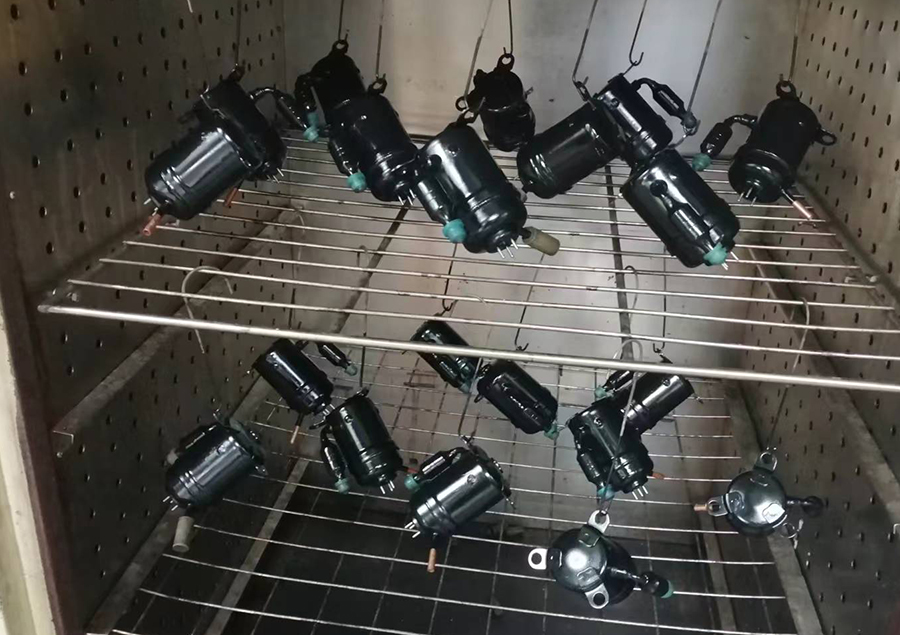
Assembly is a key process in the production of mini rotary compressors. The miniature vapor compressor assembly has high requirements in terms of equipment, technology, assembly environment, and personnel quality..
The main process flow is as follows.
Matching→valve plate riveting→pump assembly→rotor shrink fitting→housing shrink fitting→housing and reservoir welding→airtight inspection→painting→vacuum drying→online test
Special processes: housing and reservoir welding, painting
Key process: vacuum drying, online test
Conclusion
These are the steps involved in manufacturing miniature rotary refrigeration compressors. Accessory finish machining → Accessory Cleaning → Compressor assembly line → Vaccum extraction → Online test → Performance test. This manufacturing process will ensure the electric DC Compressor is reliable, efficient, and safe performance.
MOIR factory developed and manufactured a series of miniature BLDC rotary refrigeration compressors. We have a complete production process and every mobile dc cooling compressor is under strict inspection. What you get from us will be the micro & miniaturized rotary compressors, which are of uncompromised quality with spectacular cooling performance and high efficiency.
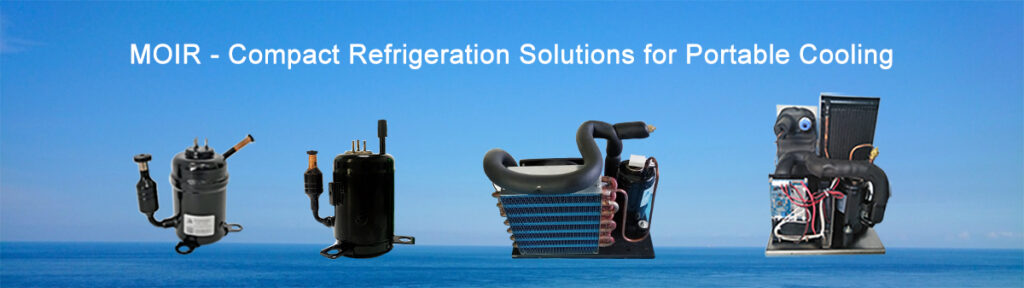