Refrigerant, also known as refrigerant working medium, is a working substance that circulates continuously in the compact refrigeration systems and realizes refrigeration through its phase change and heat transfer. The refrigerant is vaporized by releasing heat to the cooling medium in the evaporator, and the heat is absorbed to the surrounding air or water in the condenser.
This article provides ultimate guidelines for use with refrigerants R134a. Due to extreme differences that can exist in refrigeration systems, their working conditions, and duty cycles, the performance and reliability should be verified through working prototypes and field tests prior to commercial implementation.
R134a is a new type of environmentally friendly refrigerant, hydrocarbon, no damage to the atmospheric ozone layer, compared with R12 refrigerant, R134a refrigerant is non-toxic, non-combustible, stable chemical properties, thermal value is very close to R12. HFC-134a is a very effective and safe substitute for CFC-12 due to its good comprehensive performance.
It is mainly used in most fields where R12 refrigerant is used. Including: chillers, refrigerators, freezers, water dispensers, car air conditioners, central air conditioners, dehumidifiers, cold storage, commercial refrigeration, ice water machines, ice cream machines, frozen condensing units and other refrigeration equipment. Meanwhile, it can also be used in aerosol propellant, medical aerosol, insecticide ejector, polymer (plastic) physical foaming agent, and magnesium alloy protective gas.
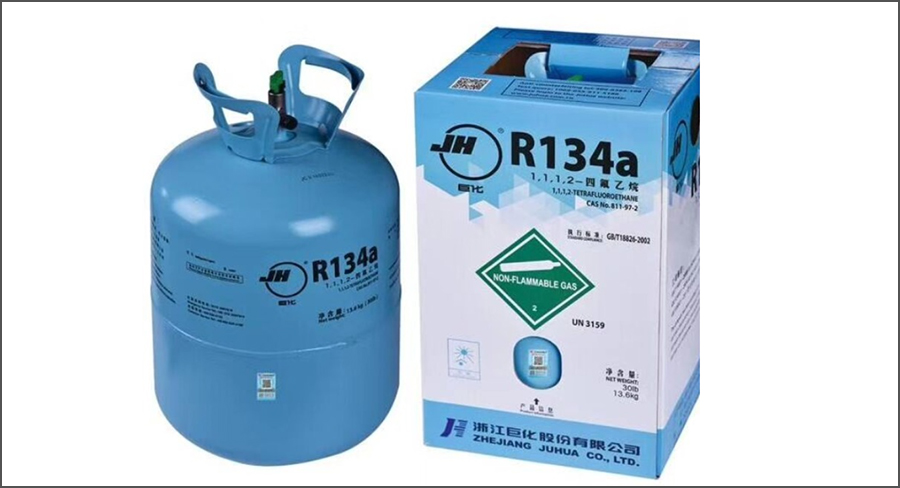
1. Technical Requirements of R134a for Components of Compact Refrigeration Systems
(1) The selection of compressor should be one level larger than the cylinder volume.
(2) The capillary should be lengthened by 10%~15%.
(3) The evaporator and condenser can remain unchanged, and the area of the condenser can be appropriately increased to reduce the condensing pressure.
(4) The amount of refrigerant charged is reduced by 10%~15%.
(5) XH-7 or XH-9 type filter dryer is adopted.
2. R134a Refrigerant Purity Technical Requirements
(1) Purity ≥99.95%
(2) Evaporation residue ≤10ppm
(3) Acid (measured by HCI)≤1ppm
(4) Water ≤10ppm
(5) CFC and HCFC≤100ppm
3. Requirements of R134a on Cleanliness, Moisture and Vacuum Technology of Refrigeration Systems
(1)Cleanliness and Water Content
① Refrigeration pipeline: Residual moisture: ≤100mg/㎡(internal surface area); Residual impurities: ≤60mg/㎡(internal surface area).
② Compressor: Residual moisture: ≤100mg/ set; Residual impurities: ≤100mg/ set.
(2) Vacuum Degree
① Unilateral vacuum pumping: the display value of the vacuum gauge ≥ 60Pa; Vacuumizing time ≥ 30 minutes.
(2) Bilateral vacuum pumping: the display value of the vacuum gauge ≥ 60Pa; Vacuumizing time ≥15 minutes.
4. New Materials and Components for R134a Compact Refrigeration Systems
(1) New material: R134a working medium; Lipid oil; XH-7 or XH-9 molecular sieve.
(2) New components: compressor with R134a; R134a Filter Dryer.
5. Manufacturing Process Requirements of R134a Refrigeration System Maintenance

(1) Compressor
R134a refrigerant is not miscible with conventional mineral compressor oil, so the compressor oil used by R134a rotary compressor is lipid oil, and the oil used by R12 compressor is mineral oil. R134a compressor internal parts design is also very different from R12 compressor, such as the compressor clearance volume, muffler mechanism, valve mechanism, motor and other parts of the material. From the technical conditions listed above, it can be seen that the residual moisture and impurities inside the R134a compressor are much stricter than the R12 compressor.
Usually, the residual moisture inside the R134a compressor is only 1/2 of the residual moisture of the R12 compressor, and the impurities are only 1/3 of the R12 compressor. Because of the strong water absorption of lipid oils, it is necessary to pay attention to that the compressor pipe opening time generally is not allowed more than 15 minutes when using R134a compressor. Therefore, if R134a refrigerant is used, use only the R134a compressor. Otherwise, the R12 compressor will decrease the refrigeration efficiency and increase the energy consumption. And there will be no cooling or lead to compressor damage after being used for a period of time,
(2) Condenser and Evaporator
The size of the processing process and volume of the condenser and evaporator using R134a refrigerant is basically the same as that using R12 refrigerant. The main technical requirements of the condenser are the residual moisture t and impurities of the condenser. In the processing process of the condenser, the use of high viscosity substances such as grease and paraffin wax should be avoided. Ester oil is required to be used. After processing, dry with nitrogen and seal both ends of the condenser with rubber plugs. The residual moisture of the inner surface of the condenser is required to be ≤50mg/㎡, and the total impurity content of the inner surface of the condenser is required to be ≤100mg/㎡. The content of soluble impurities such as mineral oil and paraffin on the inner surface of the condenser is required to be ≤40mg/m2. The content of insoluble impurities such as dust on the inner surface of the condenser is required to ≤ 60mg/㎡.
(3) Drying Filter
Conventional drying agent absorbs the refrigerant R134a while absorbing water, so specified drying agent must be used for the refrigerator that uses R134a refrigerant. The diameter of the drying agent molecular sieve of the R134 refrigerator is smaller than that of the desiccant molecular sieve of the R12 refrigerator, and in order to accelerate the speed of the drying agent absorption of moisture, under normal circumstances, R134a refrigeration desiccant usage than R12 refrigerator desiccant usage of 30%~50%. Therefore, the R12 refrigerant drying filter should not be used in place of the R134a refrigerant drying filter during maintenance.
(4) Capillary
During the processing of capillary, the connection with oil should be avoided. And the supply condition should be usually monolithic disc. The capillary must be sealed at both ends if it is supplied one by one. Because R134a refrigerant systems are more prone to oil clogging failure, the use of excessively fine capillary is generally discouraged.
6. R134a Refrigeration System Maintenance Process
If the cooling systems like a chiller, air conditioner, or refrigerator using R134a refrigerant is faulty, you need to replace a component and perform the following steps. This section uses the compressor as an example to describe how to replace other parts.
(1) Preparation before maintenance
Preparations should be made before maintenance. Because the R134a refrigerant and the lipid oil used in the compressor have strong water absorption, and the lipid oil is easy to hydrolyze, the water content and impurity in the refrigeration system should be less, and the vacuum degree should be high. Therefore, the tools and spare parts needed in the maintenance process should be prepared before maintenance, so as to quickly complete the maintenance work in the shortest time.
① Check whether the gas welding equipment and nitrogen charging device are normally available.
② Check and prepare the pumping equipment. The same equipment can be used with R600a for the evacuation equipment, but it is required to connect the rubber hose and the three-way valve, because the R134a refrigerant has corrosion effect on the rubber sealing ring. The maintenance of R134a refrigeration system requires the use of corrosion resistant connecting pipes and sealing rings. If you do not have the same connecting pipe and three-way valve as R12 for the time being, but you should check its sealing performance regularly and replace it regularly.
③ Prepare R134a refrigerant.
④ Prepare replacement parts such as filter dryer and compressor.
⑤ Prepare various tools such as clamping pliers, pipe cutters, sealing plugs, etc.
(2) Discharge refrigerant
Choose a well-ventilated space or vent the refrigerant outside. If there is no leakage in the refrigeration system, it is best to cut the capillaries with capillary pliers from the weld between the capillaries and the filter dryer to allow the refrigerant to escape through the cut in the capillaries. Discharge of refrigerant from here can play the role of cleaning the capillary, if there are impurities, oil or dirt in the capillary can be discharged by the refrigerant out. When cutting the capillary tube, be careful not to go too far away from the filter dryer, generally not more than 15mm.
(3) Remove the filter dryer and compressor
① After the refrigerant is discharged from the refrigeration system, weld the solder joints between the filter dryer and the outlet of the condenser with a welding gun, remove the filter dryer with a pliers, and put it aside to cool down (do not take it with your hands to avoid burns).
② Weld the welding spots of the upper exhaust pipe and the return pipe of the compressor respectively with a welding gun.
③ When the temperature of the exhaust pipe and return pipe of the compressor drops, remove the compressor and put it in a place other than the workplace.
(4) Clean the pipeline
① Before cleaning the pipeline, polish the high and low pressure pipe interfaces and the outlet of the condenser to remove dirt and impurities and prevent them from entering the system pipeline. (2) Connect the quick connector (Hansen valve) to the high-pressure air inlet and the low-pressure air outlet respectively, and fill 0.6-8MPa nitrogen into the evaporator and condenser respectively for cleaning. When cleaning, a clean piece of white paper can be placed at the outlet of the capillary and condenser. If there is dirt, the cleaning time should be extended until it is clean.
③ After cleaning, remove the quick connector and seal the pipe mouth with a seal. Avoid dirt and wet air from entering the pipe mouth.
(5) Install the compressor
① Secure the spare compressor to the compressor floor.
② Remove the sealing plug of the suction and exhaust pipe of the compressor, and connect the return pipe of the evaporator and the exhaust pipe of the condenser to the suction and exhaust pipe of the compressor respectively.
③ According to the welding process, welding and fixing the interfaces with a welding gun.
Noted: Do not remove the sealing plug before the compressor is welded, so as to avoid wet air entering the compressor and increasing the water content of the compressor.
(6) Install the drying filter
Cut the capillary inlet round with capillary pliers. Take out the spare filter dryer, plug the outlet of the condenser and the capillary tube into the interface of the filter dryer, and weld firmly.
Noted: The insertion of capillaries should not be too deep or too shallow, generally 13~15mm; Do not open the vacuum package before using the filter dryer. The filter dryer whose vacuum package is broken cannot be purchased or used. Because the desiccant in the dryer filter after opening the package or breaking the package has absorbed too much water, it can not only play the role of moisture absorption and drying in the refrigeration system, but also may cause the system ice jam and other failures.
(7) Nitrogen leak detection
① Remove the sealing plug on the compressor perfusion tube and weld the process tube.
② Connect the repair valve (three-way valve with vacuum pressure gauge) on the process pipe. Inject 0.8~1.0MPa nitrogen into the whole system to maintain pressure for more than 2 hours.
③ Use soapy water to detect the leakage of each solder joint or R134a leak detector to detect the leakage of each solder joint. If there is a leak point, the nitrogen should be discharged to weld the leak point again.
(8) Vacuum building
Connect the pump filling machine to the repair valve. Open the pump switch to pump out the system. The pump time should be 10~20 minutes longer than that of the R12 refrigeration system. The vacuum degree of the system should be below 100 PA. According to the weight of the refrigerant injected by the faulty machine, adjust the refrigerant scale line of the perfusion machine, turn on the charging switch, and start perfusion. After marking the standard amount of refrigerant injected according to the nameplate, close the liquid injection switch, and unload the pump perfusion machine.
Noted: If the evacuation is not thorough, the residual air and water in the system will affect the refrigeration effect; Inaccurate perfusion refrigeration effect is poor. If you do not replace the compressor, reduce the refrigerant injection amount to 90% because a small amount of refrigerant has been dissolved in the compressor. Too much perfusion will cause frosting of the trachea, too little refrigeration effect is poor.
(9) Test machine sealing
Energize compressor and observe whether the compressor runs normally. After 20-30 minutes of operation, if there is no abnormal phenomenon in the compressor, the temperature in the box begins to drop, and there is frost on the evaporator, it indicates that the system runs normally and can be prepared to seal. Use sealing pliers to clamp the middle part of the process perfusion tube.
When using the sealing pliers, the force should be uniform. Too much force is easy to clamp off the process perfusion tube. After clamping, the repair valve on the process perfusion pipe is removed, and the nozzle of the process perfusion pipe is clamped flat with clamping pliers and welded by gas welding. The sealing pliers are removed, and the clamping flat part is repaired by welding. Leak detection is required after sealing.
(10) Managing Capillary
Arrange capillary tubes in place, each pipe shall not touch each other or contact with the box; The filter dryer should be placed horizontally, or the capillary end should be tilted downward; The capillary is too close to the compressor or condenser or contact will affect the refrigeration effect.
(11) Detection
The refrigeration system shall be tested according to the testing process and shall comply with the requirements of the manual.
MOIR Refrigerant Type
Refrigerant selection can be made on the basis of availability, performance,and ecological considerations. MOIR small rotary compressors have been filled with R134a or R290 refrigerants prior to shipment. Other low-pressure refrigerants or refrigerant blends is not allowed to add.
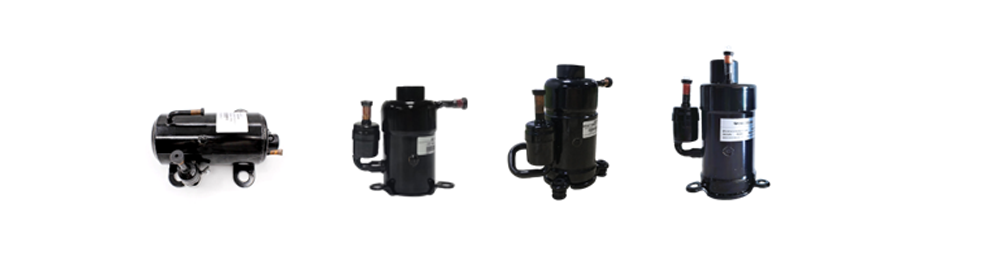
This R134a refrigerant also requires the exclusive use of polyolester oil (POE) as a lubricant. It is associated withs trict requirement for internal cleanliness of the cooling system. In addtion to chlorine and water, solid residues must be carefully removed including dust, metal particles, etc., which can damage the comrpessor. The recommend refrigerant oil is POE RL 68H. This lubricant is highly water soluble which can cause the formation of acid residues. These acid residues can create a blockage in the capillary tube and reduced lubricity in the compressor.
Therefore, all the operations related to the use of refrigerants should be conducted according to applicable regulations and engineering standards related to this article.