Introduction
In high-performance environments—whether in medical devices, laser machinery, or compact electronics—mini cooling systemsare silent workhorses. They operate behind the scenes, managing heat and preserving system stability. But like any piece of precision equipment, they demand attention. Without acooling system maintenanceplan, even the most reliable system can falter—bringing costly downtime, reduced efficiency, or permanent damage.
This comprehensive guide delivers theultimate maintenance checklist for mini cooling systems, helping you protect your investment and extend the system’s operational life.
Why Preventive Maintenance Matters for Mini Cooling Systems
Preventive care isn’t just a good habit—it’s a necessity. Mini cooling units often run 24/7 in tightly enclosed spaces. Dust buildup, worn-out fans, or minor refrigerant leaks can compound quickly, compromising performance. A consistentmini chiller maintenance schedulereduces emergency repairs, cuts energy costs, and keeps your cooling system in peak condition.
Understanding Mini Cooling Systems
Types of Mini Cooling Systems
Fromair-cooledtoliquid-cooled chillers, these systems vary in size, application, and configuration. Popular options include:
- Compact water chiller modules
- Thermoelectric Peltier coolers
- Miniature vapor-compression systems
Common Applications in Industry and Consumer Use
- Medical imaging and diagnostics
- Laser processing and engraving
- Automotive battery packs
- Beverage and food preservation
- Portable and off-grid refrigeration

Safety First: Preparing for Maintenance
Power Down and Disconnect Procedures
Before any inspection begins,completely power down the unit. Disconnect from AC/DC sources and, where applicable, isolate battery backups. Skipping this step risks electric shock or damage to internal components.
Personal Protective Equipment (PPE) Guidelines
Always wear insulated gloves, protective eyewear, and anti-static wristbands when handling electronics or refrigerants. If refrigerant access is required, make sure your workspace is well-ventilated.
Visual Inspection Checklist
Inspecting for Physical Damage
Start with a general scan. Look for dents, cracks, or signs of wear on the housing. External damage often signals internal issues.
Checking Mounting Stability and Vibration Isolation
Loose brackets, screws, or mounts can lead to excessive vibration, reducing component lifespan. Ensure vibration pads or isolators are intact and effective.
Assessing Tubing and Connector Integrity
Examinerefrigerant linesand water hoses for brittleness, discoloration, or leaks. Ensure all fittings are tight and corrosion-free.
Cleaning Essentials
Cleaning the Air Intake and Exhaust
Dust-clogged vents choke the system. Use compressed air or a vacuum to clear intake and exhaust grills.
Removing Dust from Fans and Fins
Dust-coated fans reduce airflow and cooling efficiency. Gently brush off buildup with a soft-bristle brush or air duster.
Cleaning the Condenser and Evaporator Coils
Dirty coils restrict heat transfer. Use acoil cleaner sprayor mild detergent with a soft cloth. Avoid abrasive materials that could damage fins.
Electrical Components Check
Inspecting Wiring and Connectors
Frayed wires or loose connectors can lead to erratic operation or electrical faults. Tighten and secure all connections.
Testing Relays, Fuses, and Switches
Use a multimeter to check for continuity and voltage. Replace any burned fuses or worn relays immediately.
Monitoring Power Supply and Voltage Consistency
Fluctuating voltage can impair performance. Log voltage input and ensure it stays within the system’s rated range.
Refrigeration System Maintenance
Checking Refrigerant Levels
Low refrigerant causes poor cooling and overworks the compressor. Use pressure gauges to verify proper charge levels.
Looking for Oil Stains or Refrigerant Leaks
Oil residue is often a red flag for refrigerant leakage. Inspect joints and capillary lines closely, especially in compact systems where access is limited.
Testing Compressor Performance
Listen for abnormal sounds and measure the current draw. A struggling compressor often pulls higher amps or runs hotter than usual.
Monitoring Water Flow Rate and Temperature
Forliquid-cooled chiller systems, verify that flow rate and water temperature remain within operational parameters.

Fan and Motor Maintenance
Checking for Unusual Noises or Vibration
Grinding, clicking, or humming can indicate failing bearings or unbalanced fan blades.
Lubricating Moving Parts
Apply appropriate lubricant to fan bearings or motor shafts as specified by the manufacturer.
Testing RPM and Load Balance
Use a tachometer to verify motor RPM. Inconsistent speed can indicate a failing control board or damaged motor.
Testing Display and Control Interfaces
Ensure thedigital displayis responsive. Check temperature sensors, set points, and alarm outputs. Inconsistencies could suggest a firmware or sensor issue.
Clearing Blockages and Algae Build-Up
If your system includes water circulation, flush and disinfect internal tubing to prevent microbial growth or clogging.
Software and Firmware Updates
Checking for System Updates
Consult the manufacturer’s website or support for firmware patches, especially in smart chillers or programmable logic units.
Backing Up Configuration Settings
Always save or document custom system settings before updates or resets to prevent downtime.
Environmental and Placement Considerations
Checking Ambient Operating Temperature
Mini chillers perform best within a defined temperature range. Ensure the surrounding area isn’t exceeding those limits.
Verifying Ventilation Clearance
Maintain sufficient clearance around the unit (usually 10–20 cm) to allow for optimal airflow.
Avoiding Heat Source Interference
Keep systems away from heaters, power supplies, or sunlight that could raise ambient temperatures.
Performance Benchmarking
Running Full Load and Partial Load Tests
Monitor performance under different conditions. Anomalies at full load may reveal hidden inefficiencies.
Comparing Current Performance to Baselines
Log temperature differential and power consumption over time. Compare with factory specs or historical data.
Logging Operating Parameters
Maintain a running log of inlet/outlet temperatures, flow rate, compressor duty cycle, and energy draw.
Maintenance Frequency Guide
Daily Maintenance Tasks
- Check air intake vents
- Monitor temperature output
- Listen for abnormal noises
Monthly Preventive Actions
- Clean filters and fans
- Test controls and alarms
- Inspect tubing and electrical lines
Quarterly and Annual Maintenance Schedule
- Full refrigerant and pressure check
- Electrical load testing
- Deep cleaning of coils and internal parts
- Firmware updates and sensor calibration
Common Issues and Troubleshooting Tips
Diagnosing Overheating
Could be due to low refrigerant, blocked vents, or a failing compressor.
Handling Unexpected Shutdowns
Check for tripped fuses, power supply instability, or system overheat protection.
Dealing with Noise or Vibration Problems
Verify mounts, lubricate fans, and inspect for worn bearings.
Spare Parts and Inventory Checklist
Essential Spare Components to Keep on Hand
- Fuses and relays
- Fan motors and filters
- Refrigerant fittings and hoses
- Temperature sensors
Documentation and Record Keeping
Logging Maintenance Activities
Keep detailed logs of inspections, repairs, and replacements. Use a shared cloud-based spreadsheet for easy tracking.
Tracking Performance Over Time
Over months, trends will emerge—allowing for predictive maintenance and smarter upgrades.
Outsourcing vs. In-House Maintenance
When to Use a Professional Technician
If refrigerant handling or electrical diagnostics are involved, hiring a certified technician ensures compliance and safety.
Training In-House Teams for Basic Maintenance
Many daily and monthly tasks can be handled by trained operators. Equip them with checklists and proper PPE.
Compliance and Warranty Considerations
Following Manufacturer Guidelines
Adhering to OEM maintenance schedules ensures system longevity and regulatory compliance.
Protecting Warranty with Proper Care
Improper maintenance may void your warranty. Keep service records and always use authorized parts.
Conclusion
In the world ofmini cooling systems, regular maintenance isn’t optional—it’s essential. A well-kept system runs cooler, lasts longer, and works smarter. By following thiscooling system maintenance checklist, you’ll enjoy better performance, lower operational costs, and peace of mind.
Invest inpreventive care, keep a close eye on system health, and let your cooling solution do what it does best—silently support the heartbeat of your technology.
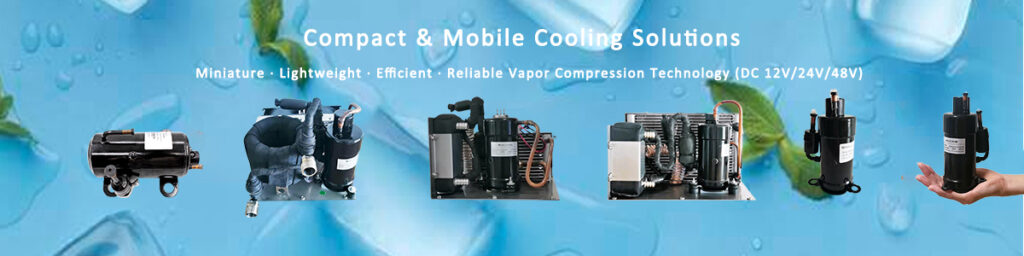