1. Introduction
The growing demand for better heat removal technologies for small-scale applications combined with the technological progress of miniature vapor compression refrigeration (VCR) components, mainly micro-compressors, and heat exchangers, has resulted in the development of compact and efficient cooling systems.
Individual components, as well as complete systems, are already increasing fast in the market and used for different cooling applications, such as electronics, chips, lasers, portable air conditioning, personal cooling, body cooling for athletes, medical applications, laboratory equipment, vehicles, farming, and other commercial and industrial applications. Due to their high energy efficiency, durability, and adequate performance in a wide range of conditions, VCR systems are considered the most promising option due to the insufficient cooling capacity of conventional passive technologies or Peltier technology for many applications.
2. What’s Miniature Vapor Compression Refrigeration System?
The vapor compression refrigeration has been proposed for compact cooling due to their high efficiency and performance. The main reason triggering their development is the fact that several of technologies, both active and passive, often have insufficient performance to satisfy the cooling needs of important applications including electronic component cooling.
Miniature refrigeration refers to systems with lower cooling capacity of 1000W than those provided by conventional units, and its purpose is to provide localized cooling at a certain place, space, system, or body demanding cooling. Compactness and lightweight are important because there is a global trend towards the miniaturization of numerous devices in different areas such as mechanics, electronics, computing, and others, and many of these devices demand refrigeration for thermal management and heat dissipation to ensure proper operation and durability.
Furthermore, compactness allows its use in applications where portable cooling systems are needed. Applications of compact cooling systems are vast and range from automotive to medical, military to aerospace, and personal to electronics cooling.
3. What’s the Components of Miniature Refrigeration System?
A compressor cooling system, whether on a small or large scale, consists of four main components, a compressor, a condenser, an evaporator, and a throttling device- expansion valve/capillary tube. The miniature compressor refrigeration system is a compact version of the traditional large compression refrigeration cycle. It operates on the same basic principles, involving the compression, condensation, expansion, and evaporation of a refrigerant to produce cooling. However, miniature systems are designed with significantly smaller components to achieve a more compact footprint.
The core components of a compact system include:
1) Compressor
The compressor is considered the heart of the refrigeration system; tasked with boosting the pressure of the refrigerant as it exits the evaporator in the form of low-temperature, low-pressure vapor. This process transforms the refrigerant into a superheated vapor at elevated temperatures and pressures. Various compressor types exist, but according to literature reports, rotary, reciprocating, and linear compressors are the most prevalent in small-scale systems. The compressor Moir offers is a kind of innovative miniature, variable speed, BLDC rotary compressor, which is the smallest compressor in the world. This mini rotary BLDC compressor would need only 1/17th of the volume, and 1/11th of the weight of a much larger & heavier conventional compressor like the reciprocating compressor, generating an equal amount of cooling while efficiently operating at up to Twice the COP.

Moir’s R&D team developed a miniature rotary variable speed compressor with size no bigger than a 250ml drink can. It was manufactured weighing less than 650g, measuring 56mm diameter and 72mm height, and designed to provide of cooling capacity of 150W at speed of 4500rpm. The speed range of the compressor is 2300rpm to 6300rpm, running with R134a and 12V-DC voltage input. To meet the changing environment and new demand in the market, we’ve engineered and developed the rotary compressor with compatibility of R290(Propane), which is the long-term green alternative to the traditional refrigerant.
Despite the challenges of compressor miniaturization, at Moir, we strive every day to develop innovative and sustainable technologies that meet the growing demand for efficient and environmentally friendly cooling solutions. Currently, we’ve offered a wide portfolio of miniature rotary compressors with cooling power ranging from 150W to 1000W. Today, they’ve been widely used in a variety of available systems for small-scale applications, where the selection will vary based on the operating conditions and, in some cases, the specific weight and dimension requirements for each application.

2) Condenser
The condenser, a type of heat exchanger (HE) used in the refrigeration loop, it transfers heat between the refrigerant at the compressor discharge (at high temperature and pressure) and the surrounding environment. The refrigerant condenses as it transfers heat to the environment, and this process occurs approximately at constant temperature and pressure, reaching a saturated or subcooled liquid state at its outlet.
In most thermal systems with space constraints, condensers are typically microchannel heat exchangers and finned-tube heat exchangers. The microchannel heat exchangers can achieve very high heat transfer rates. Plus, either as condenser, evaporators, or both, is the reduction in refrigerant mass in the compact refrigeration systems. In terms of the compactness, the microchannel condensers receive the most attention. All the condensers that are integrated into our cooling systems are microchannel type which makes them deliver features of ultra-thin size, high heat transfer rate, and reduction in refrigerant mass.

3) Throttling Devices
Throttling devices play a crucial role in the cooling process. They receive the refrigerant at the condenser outlet as saturated or subcooled liquid at high pressure and throttle it into a low pressure in an expansion process, producing a low-pressure and temperature two-phase flow.
The selection of expansion devices varies based on system requirements and conditions. Choosing an inappropriate expansion device may lead to issues such as inadequate refrigerant flow to the evaporator, resulting in liquid entering the compressor, or excessive overheating at the evaporator outlet, ultimately manifesting in poor system performance.
Capillary is one of the most commonly used throttling devices in refrigeration and air conditioning systems. A capillary is a piece of copper tube with a small inner diameter. It’s long and coiled several times, so it takes up less space. Internal diameters of capillaries for refrigeration and air conditioning applications range from 0.5 to 2.28 mm (0.020 to 0.09 in). Capillary length and diameter size are very important, they directly affect the liquid refrigeration circulation and compressor refrigeration efficiency
In the capillary, the pressure drop of the refrigerant is not due to the orifice but to the small opening of the capillary tube. The decrease in refrigerant pressure through the capillary tube depends on the diameter of the capillary tube and the length of the capillary tube. The smaller the diameter and the longer the length of the capillary tube, the greater the pressure drop as the refrigerant passes through it.
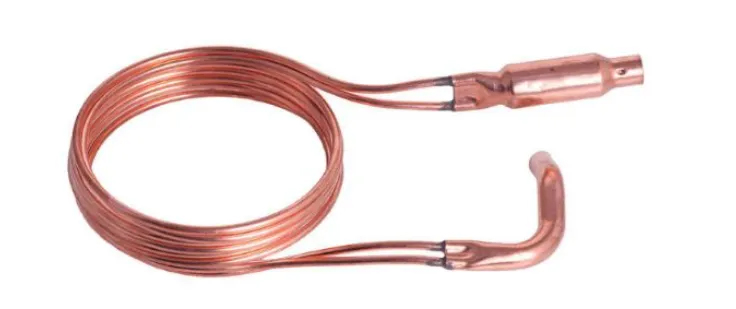
4) Evaporator
The evaporator is the cold–heat exchanger where the refrigerant removes the heating
load. It is located on the low-pressure side in the compact compressor cooling systems. At the throttling device outlet, the refrigerant is in a liquid-vapor mixture, which evaporates at low temperature and pressure as it flows through the evaporator, promoting heat transfer between the area to be cooled and the refrigerant fluid.
The use of microchannel heat exchanger as evaporators has also been quiet common, due to their compactness and high rates of heat transfer. For the small cooling systems, the evaporators that commonly be applied is stainless steel Plate heat exchangers, Coaxial stainless steel pipe, and stainless or copper oil. However, the Plate type is the one receive the most attention because of its smaller size and higher heat rates.

4. What’s the Miniature Refrigeration System Applications?
The increasing demand for enhanced functionality, higher reliability, and smaller form factor in electronic devices has driven the development of large-scale integrations and miniaturizations. Consequently, these integrations and miniaturizations have led to a consistent rise in the power consumption of electronic chips and systems. Hence, miniaturized yet powerful cooling technology is required and it has attracted the attention of many industries, such as medical, consumer, military, life science, EV, etc. Some examples include the following:
Medical sector: in portable or small-scale medical equipment, such as portable diagnostic devices, laser aesthetics treatment devices, or cooling equipment for biological samples, these systems may be necessary to ensure proper operation and accuracy of the devices.
EV Sector: in the cooling of electronic systems on board vehicles, as well as the in the thermal management of critical components ( such as battery, electronic counterparts), compact cooling systems can be beneficial due to space and weight limitation
Electronics cabinets industry: In enclosed or confined spaces may cause prone to heat build-up. Effective compact cooling system ensures optimal temperature conditions to perform reliably and space saving.
Food and pharmaceutical industry: these refrigeration & cooling systems can be essential to ensure the safety and quality of food and pharmaceutical products, especially those that require storage and transport at stable temperature.
Industrial laser industry: In sectors fluctuations in temperature can alter the laser wavelength as it travels through the optics. Spot cooling and thermal stability enables precise targeting of heat-intensive areas within a system.
Drone Docking Station sector: Drones are sensitive to temperature fluctuations and require stable environmental conditions for optimal performance and longevity. The miniature refrigeration can regulate temperature and humidity within enclosed spaces.
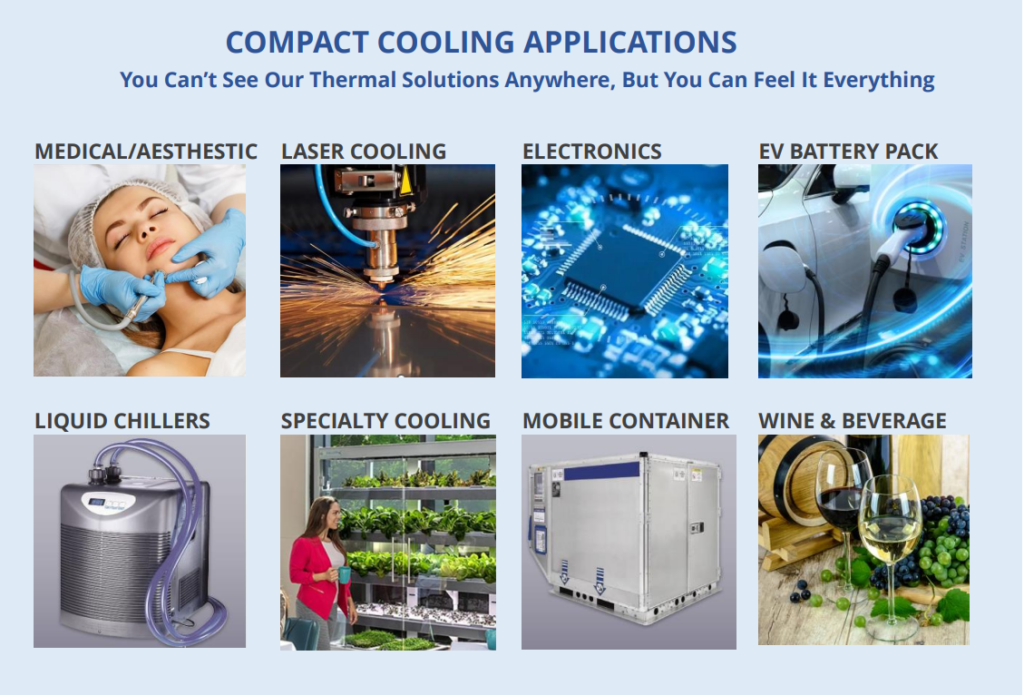
5. Future and Challenges on Miniature Refrigeration
The miniature vapor compression technology were initially developed for military purposes. As the growing demand for smaller size yet higher cooling performance in electronic devices and personal cooling devices has driven its development. Nowadays, the miniature vapor compression solutions has been used in may applications, and many more areas remain to be explored. When considering the implementation of miniature refrigeration systems in industrial environments, it is important to carefully evaluate the specific needs and constraints to ensure project success.
By adopting this small-scale compressor refrigeration system, in developed or developing areas, it is anticipated that its superior efficiency compared to other technologies will lead to significant energy savings and resultant economic benefits. Furthermore, the use of more eco-friendly refrigerants, such as R290 and R600a, enhances the sustainability of these systems, contributing to a positive environmental impact.
Because of its numerous advantages such as ultra-compact size and lightweight, working over a wide range of operating temperatures, and operation for long periods at high cooling capacity with low mass flow rates, the miniature vapor compressor refrigeration system appears to be the best option for many cooling application in limited space. However, as mentioned there are still many areas to be explored, further research and development in the miniature vapor compression sector is well warranted.
In conclusion, miniature vapor compression refrigeration systems offer a promising solution for small-scale cooling applications. With their compact size, high efficiency, and diverse range of applications, these systems are poised to play a significant role in various industries. As research and development efforts continue, we can expect to see even more advancements in this exciting field.
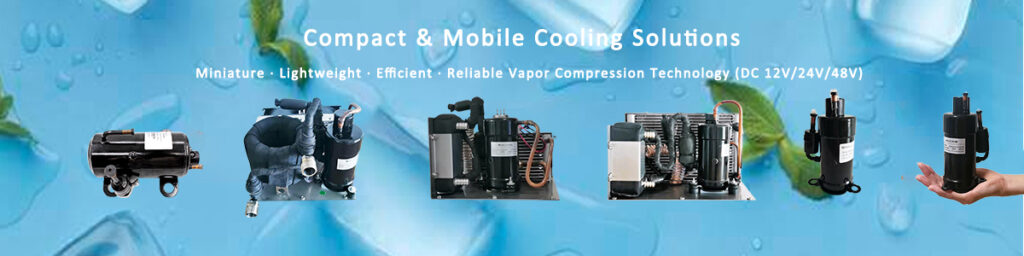